Brake, or friction pads, are a component of braking systems in equipment that needs to be slowed or stopped. People are most familiar with brake pads on automobiles, but brake and friction pads are used to slow or stop pieces of equipment like airplanes, trains, turbines, and more!
Brake Pad Composition
These pads are typically composed of a metallic backing plate with friction material bound to the surface. A braking system usually consists of two or more brake pads with friction surfaces facing a rotor.
The rotor, or brake disk, is the moving part of any brake system that slows down. When the brake pads are pushed in, like when you press the brake pedal in a car, a mechanism squeezes the two pads together onto the spinning rotor to slow and stop the vehicle.
When a brake pad heats up due to contact with the rotor, it transfers small amounts of its friction material onto the disc. The brake pad and disc then “stick” to each other, providing the friction that stops the vehicle. The friction material is the gray dust that you see deposited on the wheels of an automobile.
Selecting Brake Pad Materials
Brake pads can be made of many different materials, however, there are a few things you must take into consideration. The materials used for brake pads must:
- Compress minimally
- Be partially porous for use in wet conditions
- Withstand high temperatures without changing performance
- Balance pad and rotor wear
- Cool down quickly
- Generate minimal noise
Material selection for brake pad construction is based on the desired performance. There are several available materials and by combining them, brake pads can be made to perform for and have the correct balance for average daily driver use, heavy-duty braking needs, different environments, or even racing:
- Non-metallic
- Organic
- Semi-metallic
- Fully metallic
- Ceramic
Combining Brake Pad Materials
Specific combinations are used for vehicle weight and rotating mass.
- Organic materials tend to be softer and gentler on rotors but wear quickly.
- Composite materials that include metals have better stopping performance and heat management, but will also wear out rotors quickly.
- Fully metallic systems have even better stopping performance but will devour rotors much faster. Because of this very fast wear, fully metallic combinations are typically only used in racing applications.
Different ceramic compounds can also be added to brake pads to enhance hardness, help with heat management, and offer better grip. Graphite can be added to assist with lubrication, and phenolic-type resins are used to bind all the materials together into a “pad”.
A Recent Research Project: Confirming Brake Pad Structure and Composition
In a recent research project, we helped a university confirm brake pad structure and elemental composition. Below are images of the brake pad using different lighting techniques, and magnifications. We then use our SEM for imaging and elemental analysis (EDS). The microscope images were taken using a Leica DM2700M Materials microscope. The SEM images were taken using a COXEM E30N tabletop SEM. The EDS images were taken using an Oxford EDS detector on the COXEM tabletop/compact SEM.
The different illumination techniques can help bring out information on certain materials. For example, polarized light can highlight materials that are birefringent, and a waveplate can give more information on the axis of birefringent materials.
Bright vs Darkfield Images
Brightfield Image at 50X magnification (Leica DM2700M)
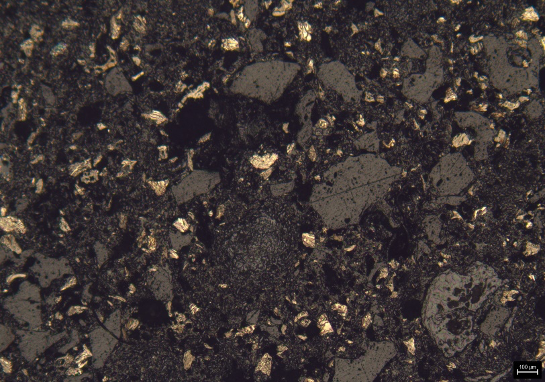
Darkfield Image at 50X magnification (Leica DM2700M)
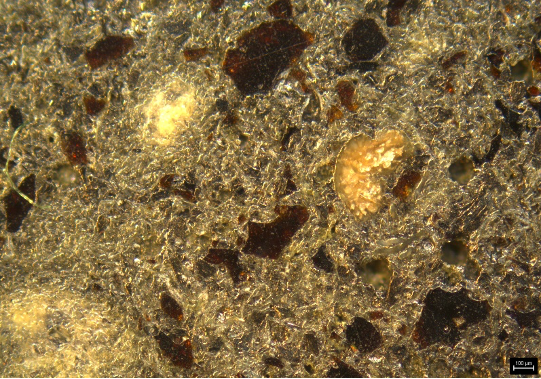
Polarized Light Images
Polarized Light at 50X magnification (Leica DM2700M)
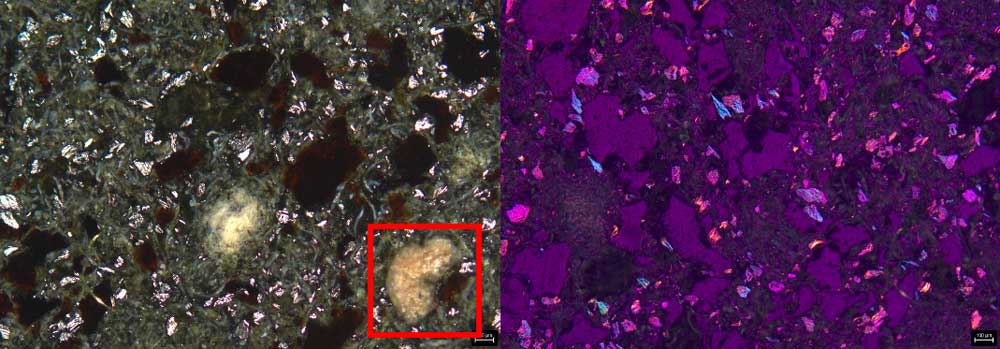
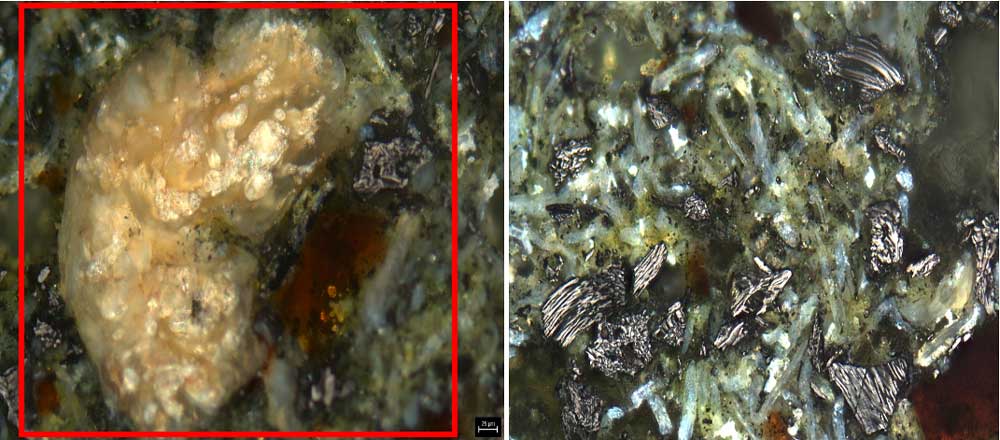
On the left, is a closer look at 200X magnification. On the right, is a graphite resin image at 200X magnification.
Graphite Resin Image at 200X magnification
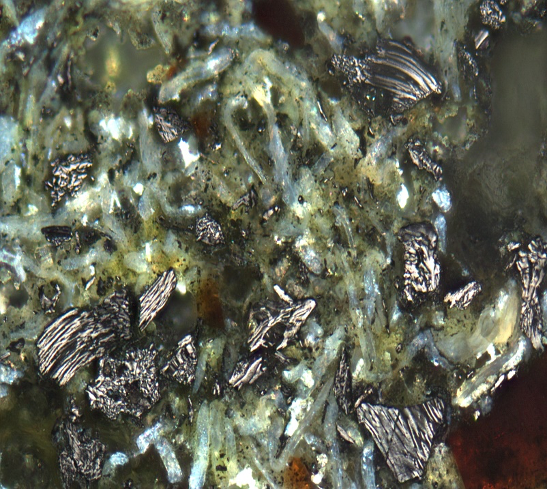
SEM Image at 500X magnification
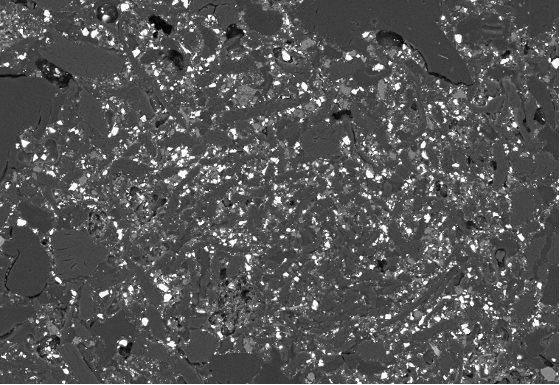
SEM Image at 1500X magnification
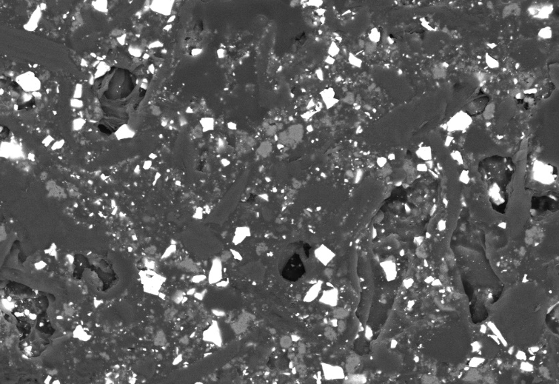
Elemental Analysis
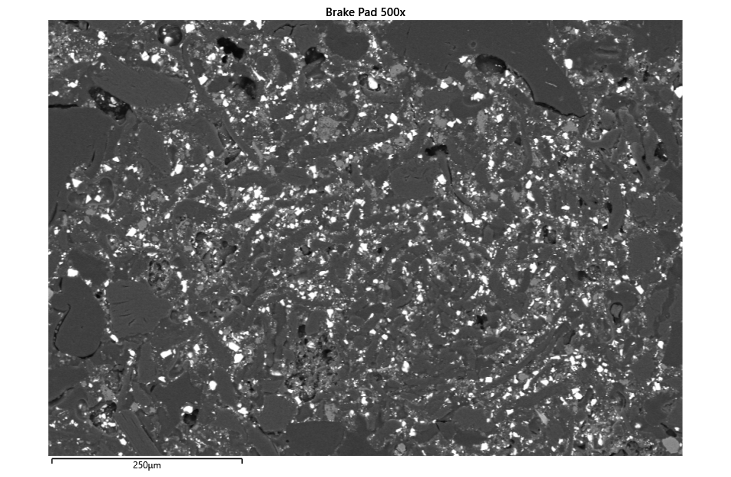
Locations of Elements
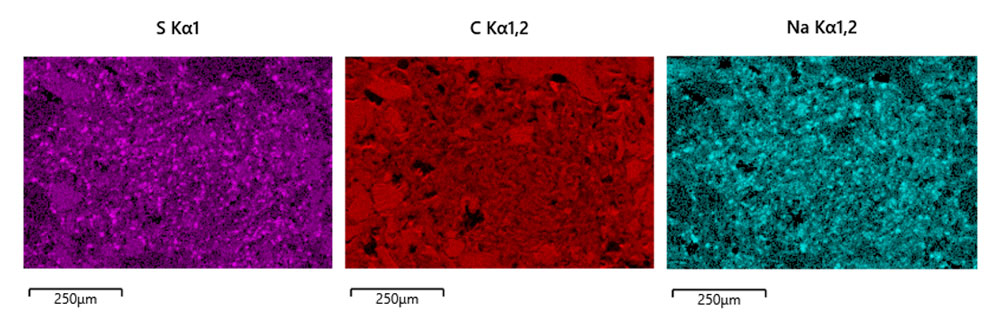
Element Chart with Percentage Distribution
Element | Line Type | k Ratio | Wt% | Wt% Sigma | Atomic % |
---|---|---|---|---|---|
O | K series | 0.04132 | 17.31 | 0.12 | 32.03 |
F | K series | 0.03492 | 17.41 | 0.13 | 27.13 |
Na | K series | 0.02725 | 12.54 | 0.07 | 16.15 |
Mg | K series | 0.00103 | 0.41 | 0.04 | 0.5 |
Al | K series | 0.0212 | 6.76 | 0.05 | 7.42 |
Si | K series | 0.00768 | 2.01 | 0.03 | 2.12 |
S | K series | 0.03128 | 6.54 | 0.05 | 6.04 |
Cl | K series | 0.00284 | 0.58 | 0.03 | 0.48 |
K | K series | 0.00187 | 0.33 | 0.03 | 0.25 |
Ca | K series | 0.00169 | 0.28 | 0.03 | 0.21 |
Fe | K series | 0.00075 | 0.13 | 0.04 | 0.07 |
Cu | K series | 0..00127 | 0.21 | 0.06 | 0.1 |
Pd | L series | 0.02606 | 5.18 | 0.08 | 1.44 |
Ba | L series | 0.12202 | 22.99 | 0.11 | 4.96 |
Au | M series | 0.03498 | 7.32 | 0.14 | 1.1 |
Data from scan showing EDS chart with elements present in the sample:
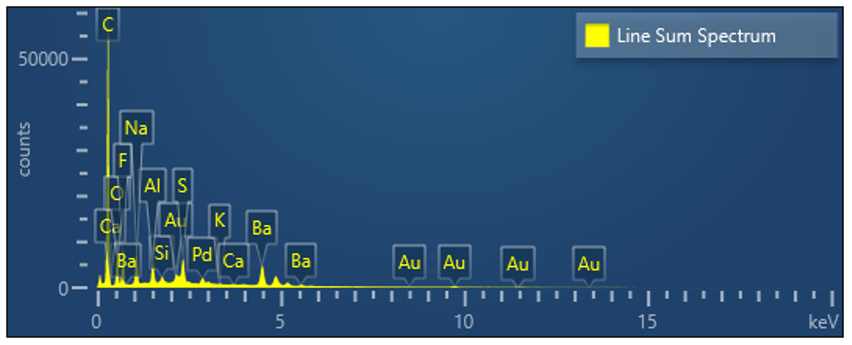
By looking at the data from the EDS maps, we can see what looks like Barium Sulfate and some material that is a combination of Sodium, Fluorine, and possibly Aluminum plus lots of Carbon.
The optical images show graphite, probably used as a lubricant, and also show multiple polymers, ceramics, and metal alloys in the “mix”.
These ratios are critical in understanding the capabilities of this particular braking material.
The different optical inspection, electron microscopy inspection, and elemental analysis data will help to understand and confirm that the correct combination of materials was achieved.
In this case, the brake pad was new. A used brake would also give us information on wear, heat damage, and other relevant points of data.
All of the analysis tools used in this application are part of JH Analytical’s lab equipment infrastructure. If you are curious about this application or would like more details please contact us using the contact form.