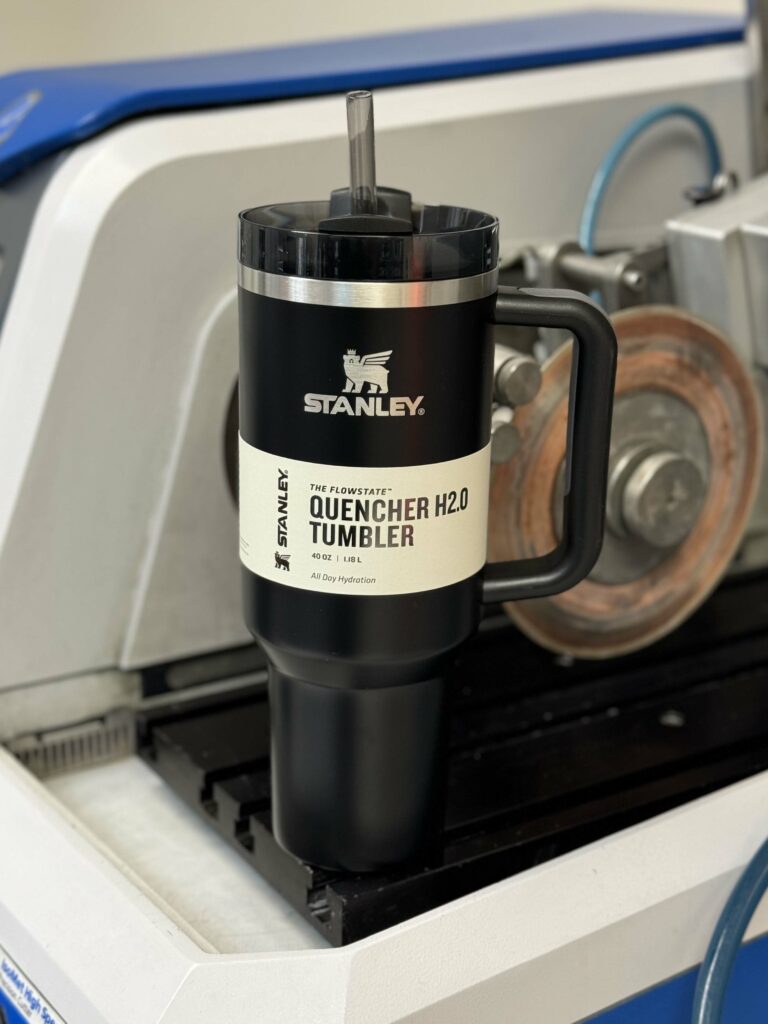
Recent concerns about lead in Stanley Tumblers have sparked public interest and debate. While many sources suggest there’s no need to worry, concrete scientific data has been lacking. To address this, we conducted a thorough scientific investigation to provide consumers with accurate information for informed decision-making.
Methodology
Our team of scientists and materials engineers employed a comprehensive approach to examining the Stanley Tumbler. This included visual inspection, precision disassembly, optical microscopy at 10x magnification, Scanning Electron Microscopy (SEM), and Energy Dispersive X-ray Spectrometry (EDS).
These methods allowed us to thoroughly analyze the tumbler’s composition and structure.
Findings
We identified the tumbler’s base as the area of interest through online research and physical examination.
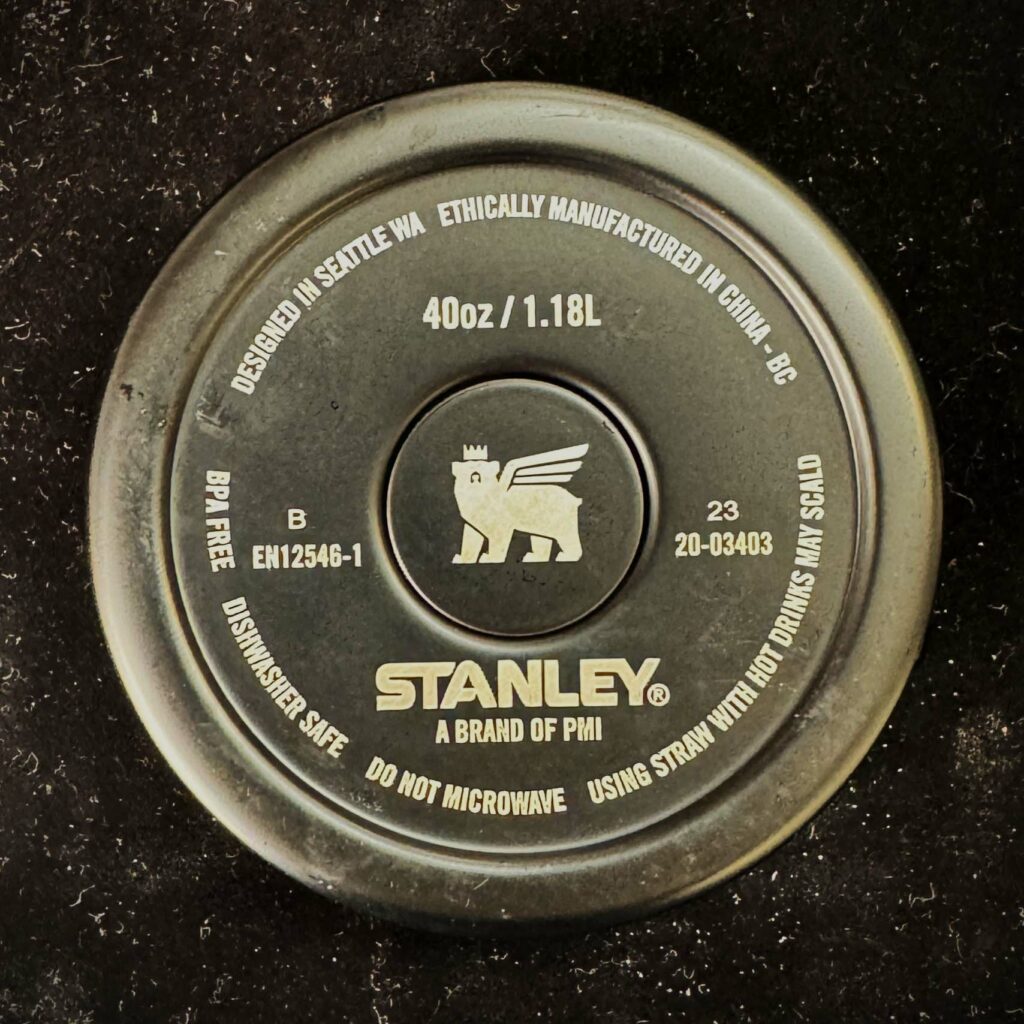
Upon disassembly, we found a small hole in the center of the bottom, visible in Figures 2A and 2B. This hole is used to inject a lead alloy under controlled temperature, creating a vacuum seal crucial for the tumbler’s ability to maintain temperature effectively.
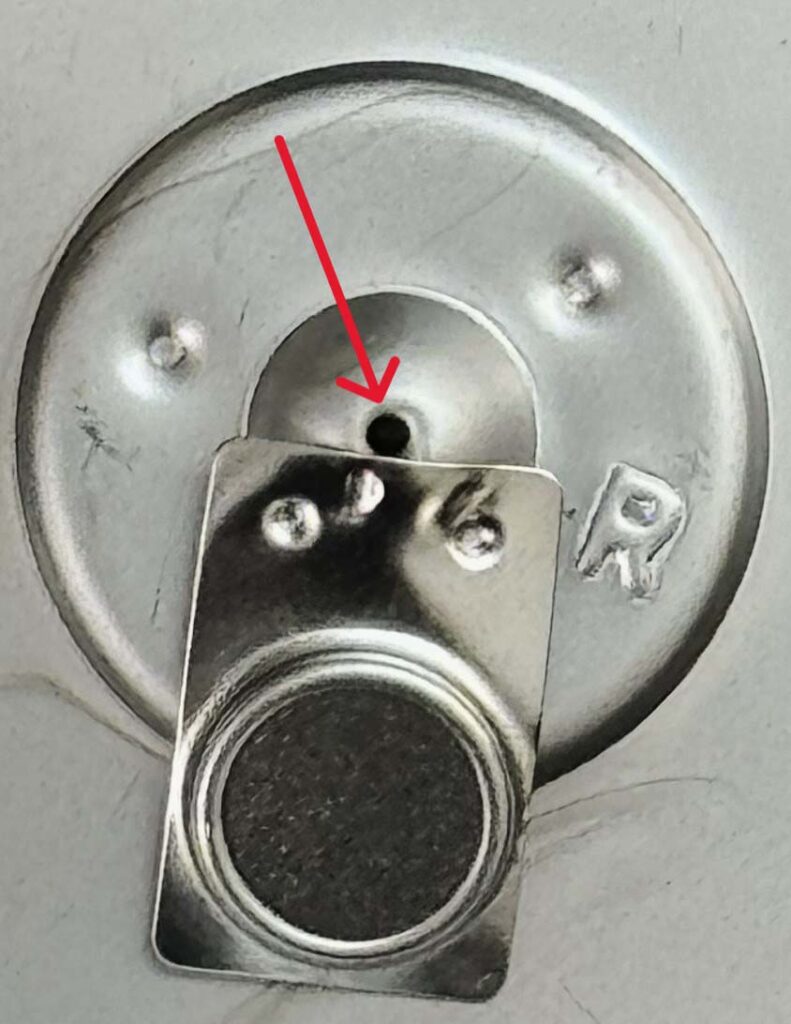
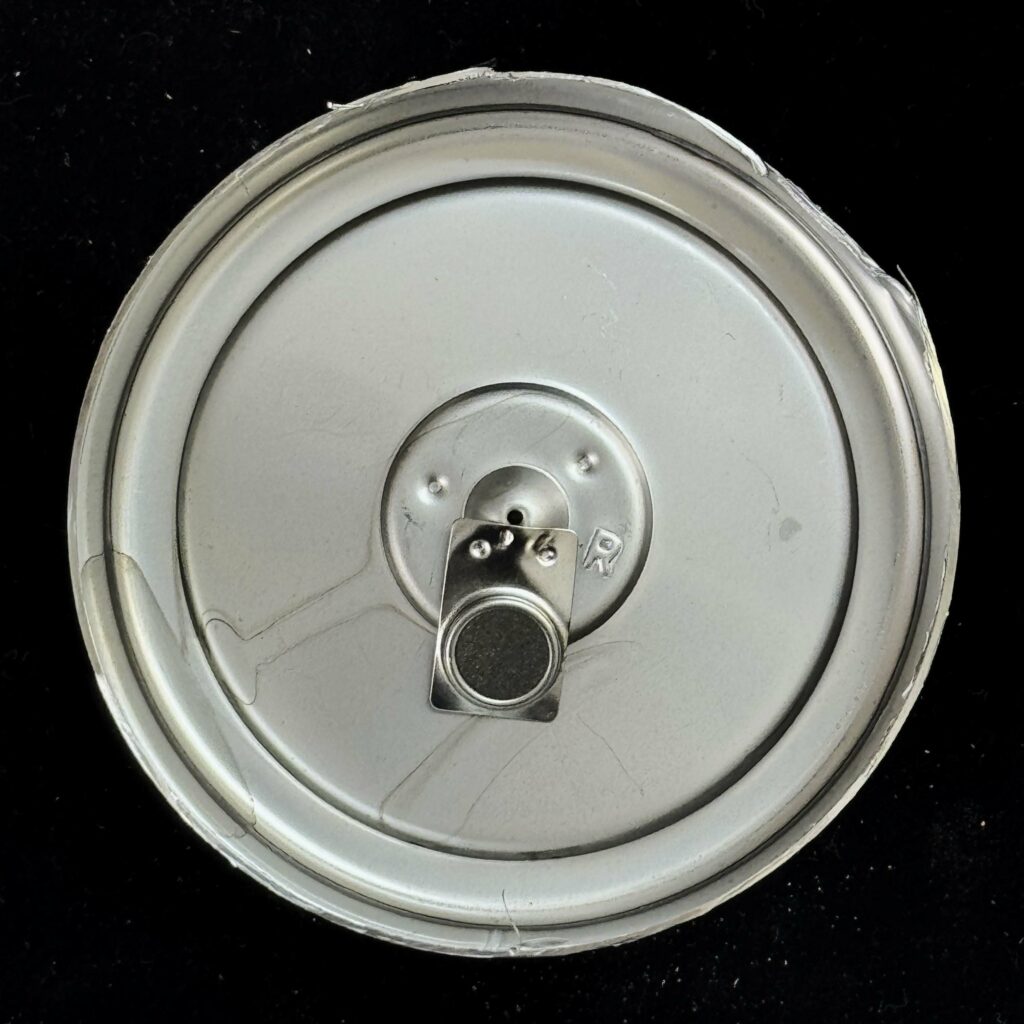
Cross-sectioning the cup revealed the sealing area, which is visible both to the naked eye and under an optical microscope, as shown in Figures 4 and 5.
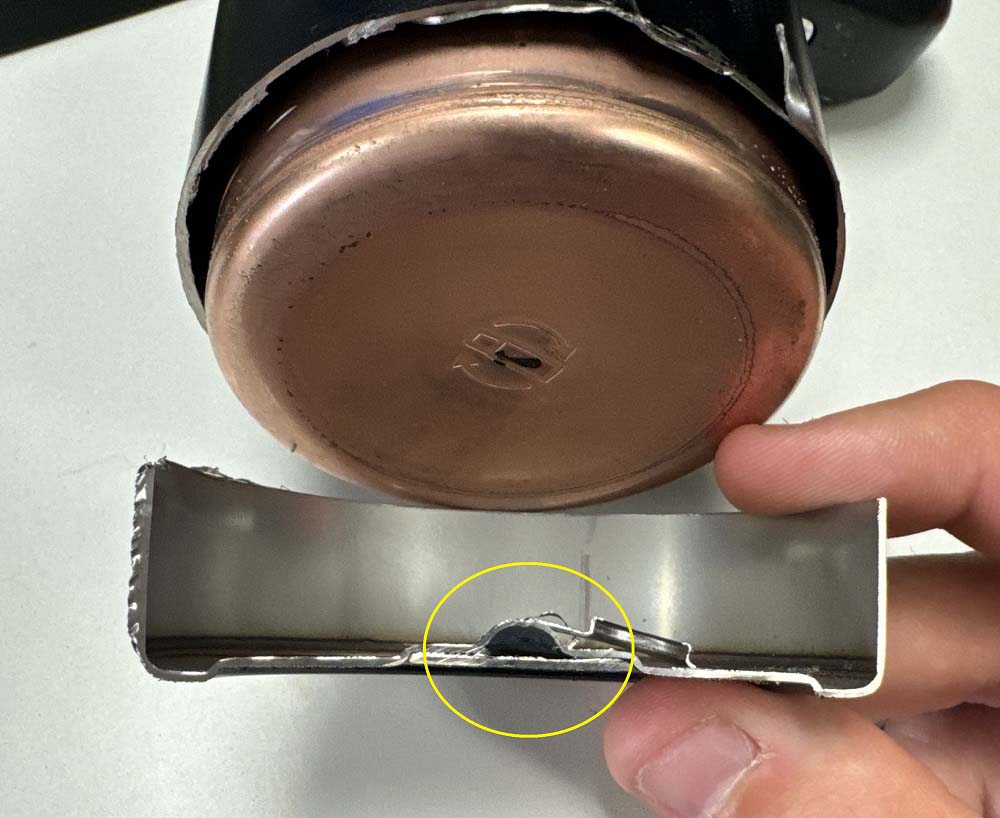
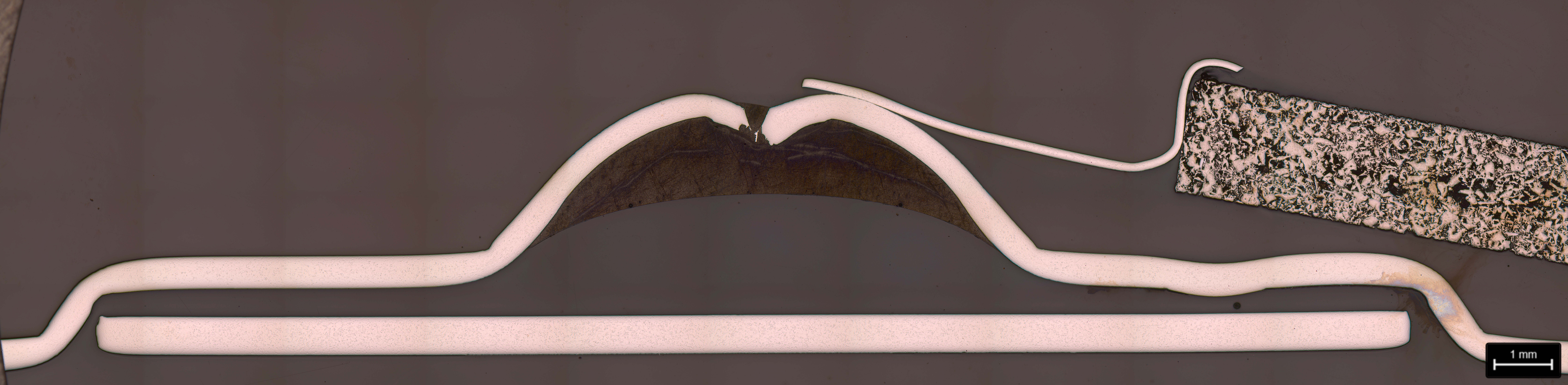
Further examination using SEM with Energy Dispersive X-ray Spectrometry (EDS) confirmed the presence of a lead alloy (Figures 6 and 6A).
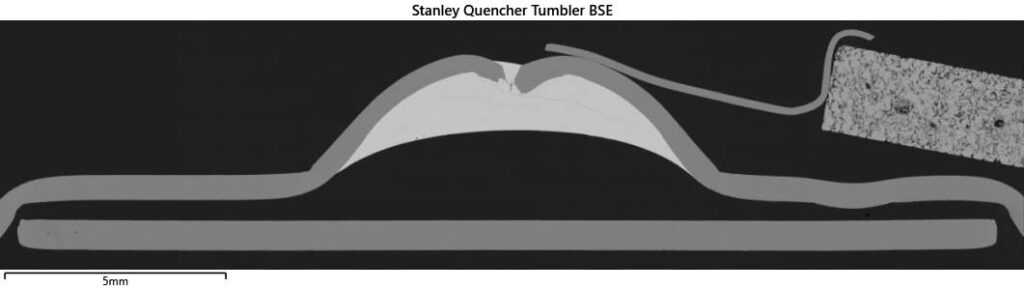
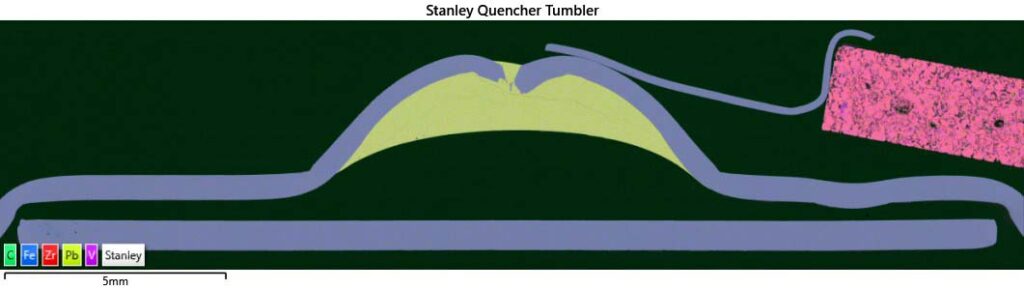
Our findings align with Stanley’s official statement: “Our manufacturing process currently employs the use of an industry-standard pellet to seal the vacuum insulation at the base of our products; the sealing material includes some lead. Once sealed, this area is covered with a durable stainless-steel layer.”
The lead alloy does not contact drinking areas or touchpoints under normal use. The FDA still considers this manufacturing process safe, and no incidents of lead exposure from Stanley Tumblers have been reported despite decades of use.
Discussion
Lead is used in this process because it is cost-effective and has properties ideal for creating airtight seals. It’s soft and pliable, making it perfect for solidifying the vacuum seal in the dual-layer stainless steel shell. While the likelihood of consumer exposure is extremely low, questions remain about long-term disposal and recycling practices and potential exposure to workers during manufacturing.
Although lead-free alternatives exist, switching to these would likely increase production costs and consumer prices. This presents a challenge for the industry in balancing safety concerns with economic considerations.
Conclusion
Our investigation confirms the presence of lead in Stanley Tumblers but demonstrates that the risk to consumers is minimal under normal use. The greater risk seems to be to the workers producing these products, which raises broader questions about manufacturing ethics, particularly regarding worker safety during production.
Environmental impact is another consideration, as proper disposal and recycling of these products are important for long-term safety. The industry faces a challenge in balancing production costs with completely lead-free alternatives.
While our findings provide reassurance for consumers, they also highlight the need for ongoing discussions about manufacturing practices, environmental responsibility, and the cost of safer alternatives in consumer products. As technology and materials science advance, it’s crucial to continually reassess and improve manufacturing processes to ensure consumer safety, environmental stewardship, and corporate sustainability. It’s got to be a Win! Win! Win situation!
Thanks to our talented lab team, Will Bond, SEM Engineer, and Ayrton Sierra, Materials PhD., for their work on this project.