This month, JH Analytical took a deeper dive into a critical, wear-prone component in nearly all internal combustion-powered vehicles: the camshaft.
The camshaft’s purpose is to time and mechanically open and close the valves, which, in this case, dictate the 4-stroke cycle: intake, compression, combustion, and exhaust.
Camshaft Materials and Manufacturing
The camshaft of a 4-stroke engine rotates in sync with the crankshaft at a ratio of 2:1, respectively, which yields up to 3,500 rpm at “redline” in a typical street vehicle. However, some camshafts can exceed 10,000 rpm.
Because the camshaft is in regular physical contact with rocker arms (or pushrods), the material used to make them must resist abrasion, deformation, and extreme physical stresses brought on by rapid rotation in a high-temperature environment. While you can use other materials, cost, ease of manufacturing, and reliability prove cast iron is the most common material. In addition, using cast iron allows automotive manufacturers to leverage abundant metallurgical processes and research to achieve the exact properties needed.
Sample Preparation for EBSD: Camshaft Sectioning and Mounting
JH took a field trip to the scrapyard (again) to pick up a mid 90’s Honda Civic camshaft.
- First, we sectioned a portion of the camshaft using a Buehler IsoMet Highspeed Pro saw with a cubic boron nitride blade.
- Then, we encapsulated the sample using a Buehler SimpliMet 4000 compression mounting system. Compression mounting yields a harder encapsulant, resulting in better edge retention when grinding and polishing hard materials.
- Finally, we performed the grinding and polishing procedure with a Buehler AutoMet 250 to achieve an optimal surface for Electron Backscatter Diffraction (EBSD).
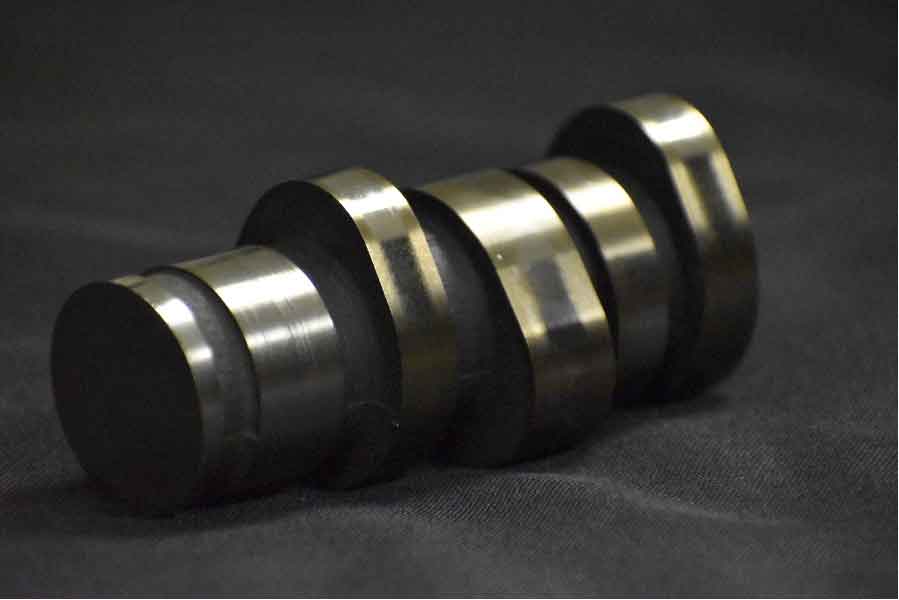
EBSD Analysis Results
Using a ThermoFisher Apreo S SEM, we mounted the sample and collected characteristic x-rays to map out the constituent elements using Energy Dispersive X-Ray Spectroscopy (EDS) (Oxford UltiMax100). See fig.1
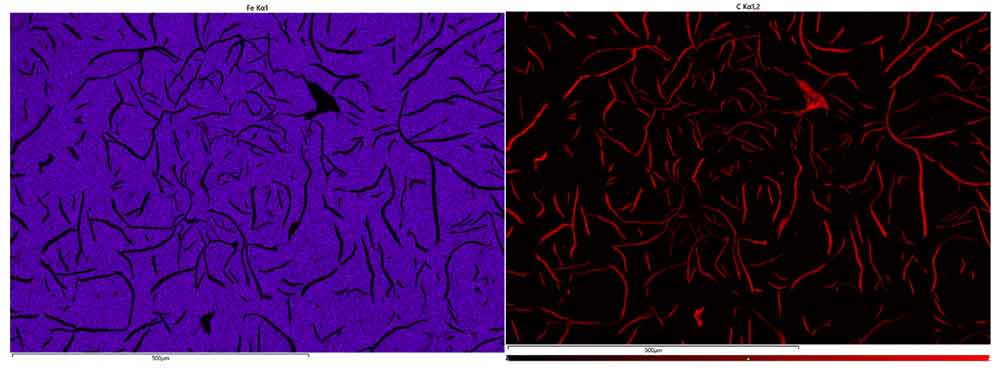
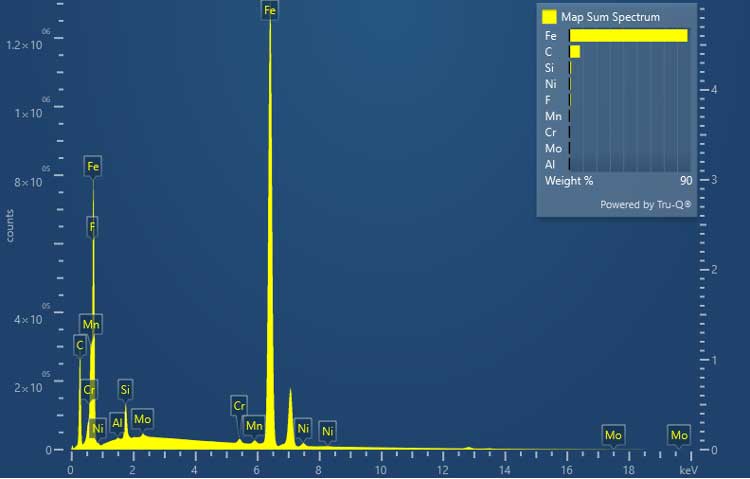
Based on the elemental composition, we identified potential phases to enter into the EBSD software, then began phase mapping. The data we collected indicated that the scanned region was not hardened after casting and was left in a phase of iron known as austenitic pearlite.
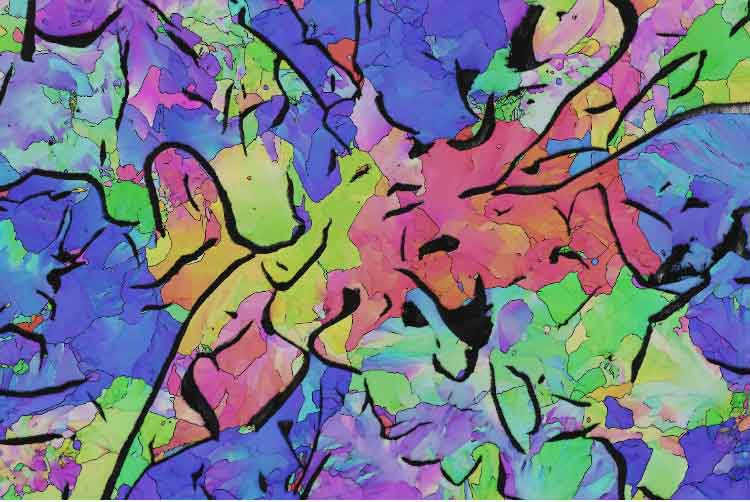
Pearlite has physical characteristics that make it suitable for high-stress applications due to the carbon present as crystalline graphite within the eutectoid structure. Process variables like cooling rate or local hardening can create different iron phases within the same camshaft. For example, along the camshaft lobes, which are in regular contact with stationary components during high-speed rotation, a harder phase, like cementite, is typically due to its abrasion resistance. Accelerated local cooling in these lobed regions achieves this phase.
Importance of Metallurgical Analysis for Automotive Applications
Metallurgical analysis is a critical tool for automotive manufacturers and suppliers looking to prolong the lifetime of complex mechanical systems like engines, transmission, and suspensions. Microstructure analysis via EBSD is key in identifying crystalline phases, composition, and residual stresses trapped within materials which can significantly alter physical properties. Rapidly identifying defects through EBSD improves processes and prevents premature failure of components, ensuring a satisfied end user and a safe, reliable product.
Need help with Metallurgical Analysis for your application?
Complete the form on this page or contact us.