Achieving an ideal balance of wear resistance and flexibility is a challenge that metallurgists have faced for centuries. With the advancement of refining and alloying processes, novel methods of optimizing these properties have continued to emerge. In JH Technologies’ latest application note, learn about case hardening and measuring and analyzing samples.
What is Case Hardening?
Case hardening, also known as surface hardening, hardens the outer metal surface of a finished or near-finished product while maintaining a soft and malleable core. In the case of modern steel, the first step of case hardening is exposing components to a carbon-rich environment at high temperatures. During exposure, the steel surface absorbs carbon and rapidly quenches it in a carbon-rich fluid such as oil (carburizes).
Induction heating involves only steel heating and rapid cooling to create a “casing” of martensite. Both cases produce a wear-resistant surface without the associated increased fracture risk under heavy loads in the final product. The automotive industry, agricultural machinery, and manufacturing equipment commonly employ these and other variants of case hardening.
Case Hardening Measurement and Verification
We recently acquired a conveyer belt roller typically used in food production and agriculture. These rollers must sustain extreme loads up to 24 hours a day without deforming or abrading to minimize costly maintenance, repairs, and downtime. As a precaution, manufacturers will periodically monitor and measure the wear on rollers to anticipate their lifespan. By measuring the depth of case hardening and monitoring wear, you can power down large-scale systems for preventative maintenance.
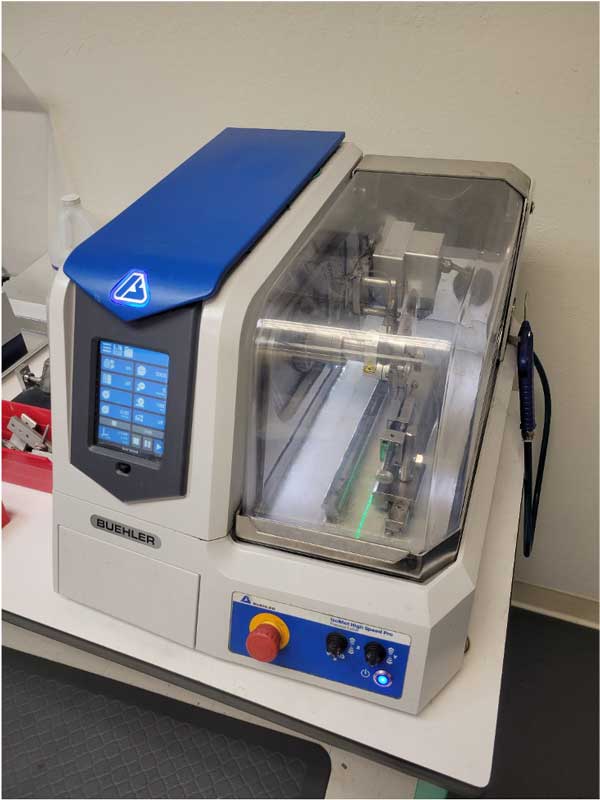
Analyzing Case-Hardened Components
The first step in analyzing a case-hardened steel component is cutting the sample with a liquid-cooled saw. If the sample does not cool effectively during cutting, the blade’s friction can heat the sample, deforming the grains or hardening the surface. Both outcomes can negatively impact data quality. We cut the roller using a 7-inch diamond blade in a Buehler IsoMet High-Speed Pro.
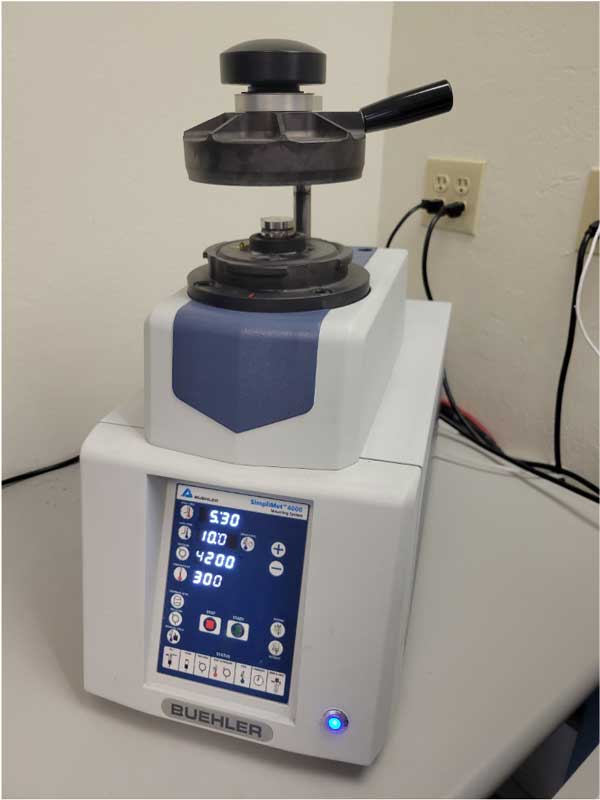
After cutting, we potted the sample using Buehler SimpliMet 4000 compression mounting system. Although you can use a standard, two-part epoxy (EpoxiCure 2), using mineral-enriched polymers (EpoMet) for compression mounting results in a harder encapsulant. This hardness is critical to edge retention during metallurgical sample preparation.
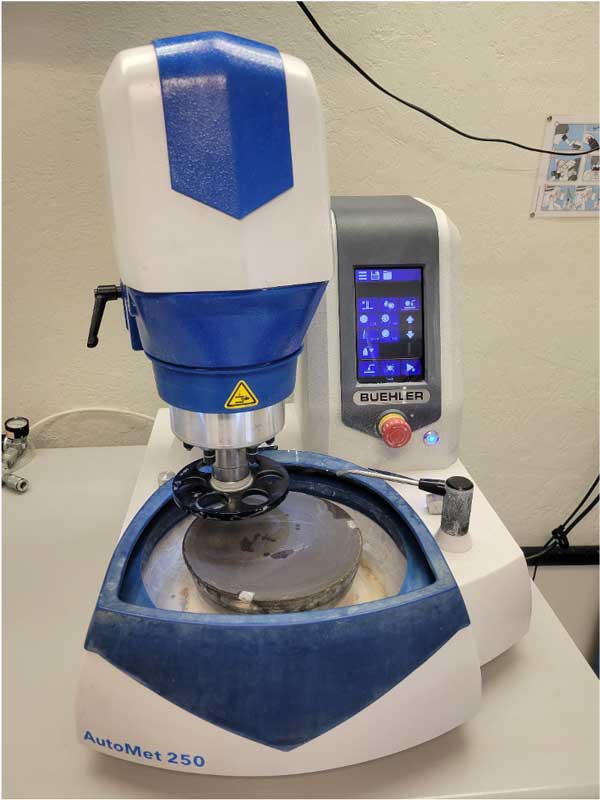
Next, we mechanically polished the encapsulated roller portion using progressively finer diamond grinding discs and monocrystalline diamond suspensions on a Buehler AutoMet 250.
Once we achieved a suitable finish, we tested hardness using a Wilson VH1202 with a Knoop indenter. While the system can perform Vickers and Knoop hardness testing, some metallurgists prefer Knoop as their standard.

We collected hardness data at ten locations perpendicular to the hardened sample surface. The first location was 5mil (127µm) from the sample edge, and all subsequent locations were 5mil apart. We pressed the indenter into the polished surface at each location with a test force of 50 grams. Next, we retracted the indenter, measured the indentation, and directly translated the dimensions into hardness values.
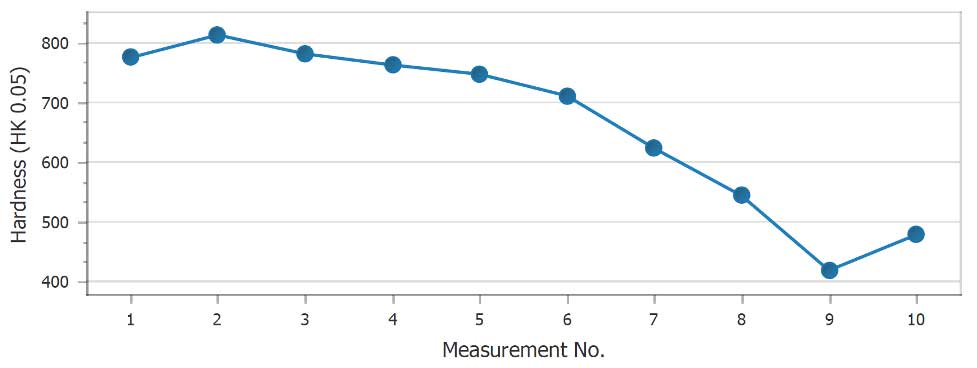
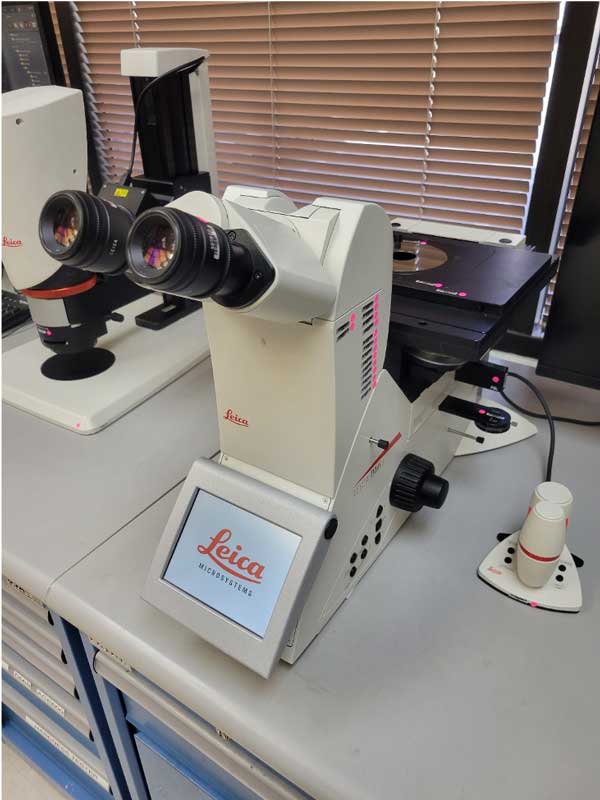
After additional polishing to remove the indentations incurred during hardness testing, we etched the sample using a solution of ~4% nitric acid in ethanol, commonly called nital or temper etch. Nital preferentially etches certain steels to reveal grains, microstructures, and inclusions. Etching emphasizes these microstructures by topography, facilitating inspection using only a standard optical microscope. We etched these grains into our sample using a Leica DMi8 inverted microscope.
Case Hardening Results
At a magnification of 100x, the microstructure of the case-hardened steel roller is immediately evident.
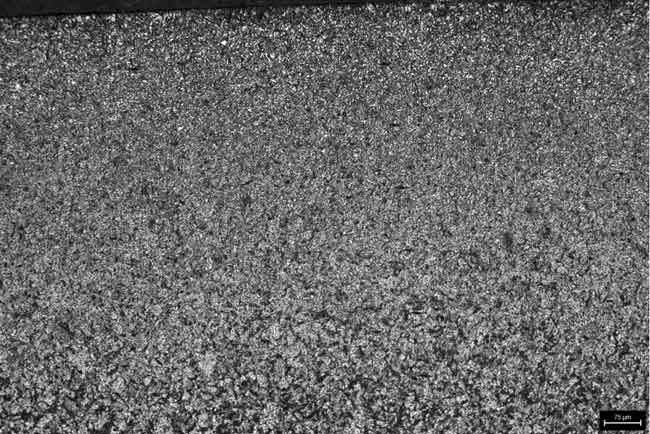
At 500x magnification, we can clearly distinguish the microstructure of the case-hardened region from the bulk.
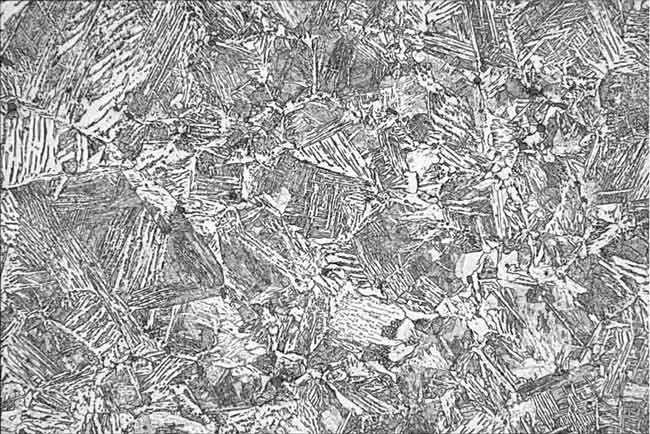
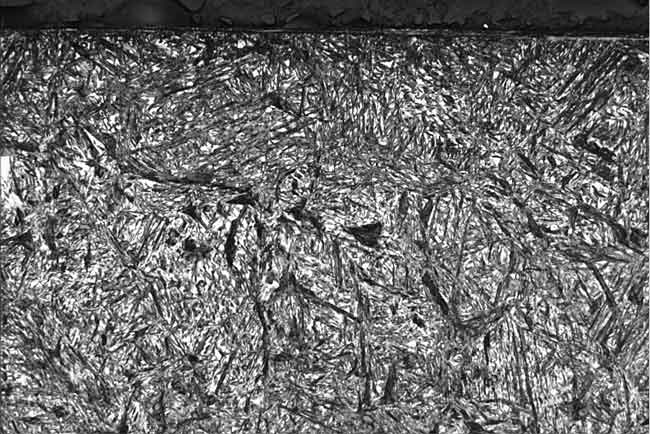
Case Hardening in the Future
Crude case hardening techniques, found in texts dating back over 3,000 years, remain an area of focus across multiple industries. In addition to optimizing known processes, metallurgists continue investigating novel methods and materials to get the most out of their products at the lowest costs. We can apply nitriding as an example of a case hardening method to certain steels as well as titanium, aluminum, and molybdenum.
Case hardening has accelerated human progress in many fields over millennia, from food production to transportation and beyond. As people discover new alloys, polymers, and other novel materials, they continue to employ case hardening on a large scale to support the ever-growing population. Although case hardening may become obsolete in the future, the current scale of its utilization ensures that it will be around for a long time.
Need help with Hardness Testing for your application?
Complete the form on this page or contact us.